Pavement
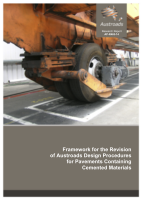
- Publication no: AP-R463-14
- ISBN: 978-1-925037-73-9
- Published: 27 June 2014
- PDF (free) Download
The laboratory characterisation of cemented materials for road pavements was completed in Austroads Project TT1359 Cost-Effective Structural Treatments for Rural Highwaysand more recently in Austroads Project TT1664 Cemented Materials Characterisation.
These projects concluded there is a need for a substantial revision to the thickness design procedures for cemented materials as provided in Austroads Guide to Pavement Technology Part 2: Pavement Structural Design(AGPT02-12).
This report reviews the origins of the current design procedures and the results of past and recent laboratory and accelerated loading trials on cemented materials modulus and fatigue. A framework for the revision of the design of flexible pavements containing cemented materials is proposed.
- 1. Introduction
- 2. 1987 NAASRA Guide
- 3. VicRoads Adopted 8th Power Relationship
- 3.1. Original Analysis and Conclusion
- 3.1.1. Laboratory Fatigue Relationship
- 3.1.2. Field Fatigue Relationships
- 3.2. Further Analysis
- 4. 1997 Change to 12th Power Relationship
- 5. Austroads Project TT1065 Findings
- 5.1. Introduction
- 5.2. Laboratory Testing
- 5.2.1. Moduli and Breaking Strains
- 5.2.2. Fatigue
- 5.3. Fatigue Under Accelerated Loading
- 5.3.1. Introduction
- 5.3.2. Findings without Considering Variability between Test Sections
- 5.3.3. Analysis Considering Variability between Test Sections
- 5.3.4. Usefulness of Stress-based Fatigue Relationship
- 6. Summary of Findings from Recent Laboratory Testing
- 6.1. Introduction
- 6.2. Flexural Moduli of Laboratory-manufactured Beams
- 6.3. Breaking Strain and Flexural Strength
- 6.4. Individual Laboratory Fatigue Relationships
- 6.5. Fatigue Life Dependence on Modulus, Breaking Strain and Flexural Strength
- 6.5.1. Strain at 105 Cycles Variation with Modulus, Strength and Breaking Strain
- 6.5.2. Stress at 105 Cycles Variation with Flexural Strength
- 6.6. Effect of Micro-cracking on Fatigue Life
- 6.6.1. Introduction
- 6.6.2. Change in Fatigue Life with Condition State
- 6.6.3. Review of Past Accelerated Loading Results
- 6.7. Summary of Findings
- 7. Comparison of Laboratory and Field Fatigue
- 7.1. Introduction
- 7.2. Extrapolation of Laboratory Results
- 7.3. Ability of the Laboratory Fatigue Test to Rank Materials
- 7.4. Interim Tolerable Strain Shift Factors
- 7.4.1. Introduction
- 7.4.2. Critical Condition State that Limits In-service Fatigue Life
- 7.4.3. Review of Laboratory Micro-cracking Study Findings
- 7.4.4. Review of Accelerated Loading Data Findings
- 7.4.5. Interim Shift Factor
- 7.5. Limits on the Tolerable Strains and Fatigue Constants
- 7.6. Examples of In-service Fatigue Relationships
- 7.7. Summary
- 8. Proposed Procedures to Determine the Design Moduli of Cemented Materials
- 8.1. Introduction
- 8.2. Definition of Design Modulus
- 8.3. Design Moduli from Laboratory Flexural Beam Tests
- 8.3.1. Adjustment of Mean Laboratory Modulus to Mean In Situ Modulus
- 8.3.2. Adjustment of Mean In Situ Modulus to Characteristic Value
- 8.3.3. Adjustment for Density
- 8.3.4. Maximum Design Modulus
- 8.3.5. Examples of Cemented Material Moduli
- 8.4. Estimation of Laboratory Flexible Modulus from Unconfined Compressive Strength
- 8.5. Presumptive Design Moduli
- 8.5.1. Pre-cracking
- 8.5.2. Post-cracking
- 9. Proposed Fatigue Characterisation Procedures
- 9.1. Introduction
- 9.2. Summary of Key Research Findings
- 9.3. Condition at the End of Fatigue Life
- 9.4. In-service Fatigue Relationships from Laboratory Fatigue Testing
- 9.4.1. Introduction
- 9.4.2. Laboratory Fatigue Measurement
- 9.4.3. Fatigue Constant k of Laboratory Fatigue Relationship
- 9.4.4. Laboratory-to-field Strain Shift Factor
- 9.4.5. Fatigue Constant K of the In-service Fatigue Relationship
- 9.4.6. In-service Fatigue Relationship
- 9.4.7. Example Fatigue Relationships
- 9.4.8. Example Design Thicknesses
- 9.5. In-service Fatigue Relationships from Measured Flexural Modulus and Flexural Strength
- 9.5.1. Introduction
- 9.5.2. Determination of Design Flexural Modulus and Design Flexural Strength
- 9.5.3. In-service Fatigue Relationship
- 9.5.4. Example Design Thicknesses
- 9.6. Presumptive Fatigue Criteria
- 9.6.1. Introduction
- 9.6.2. Presumptive Flexural Strengths
- 9.6.3. In-service Fatigue Relationships
- 10. Conclusions
- References